Parlare al giorno d’oggi di motori diretti, o direct drive, è in molti settori dell’automazione industriale una tecnologia assodata mentre questa tipologia di motorizzazioni trova sempre […]
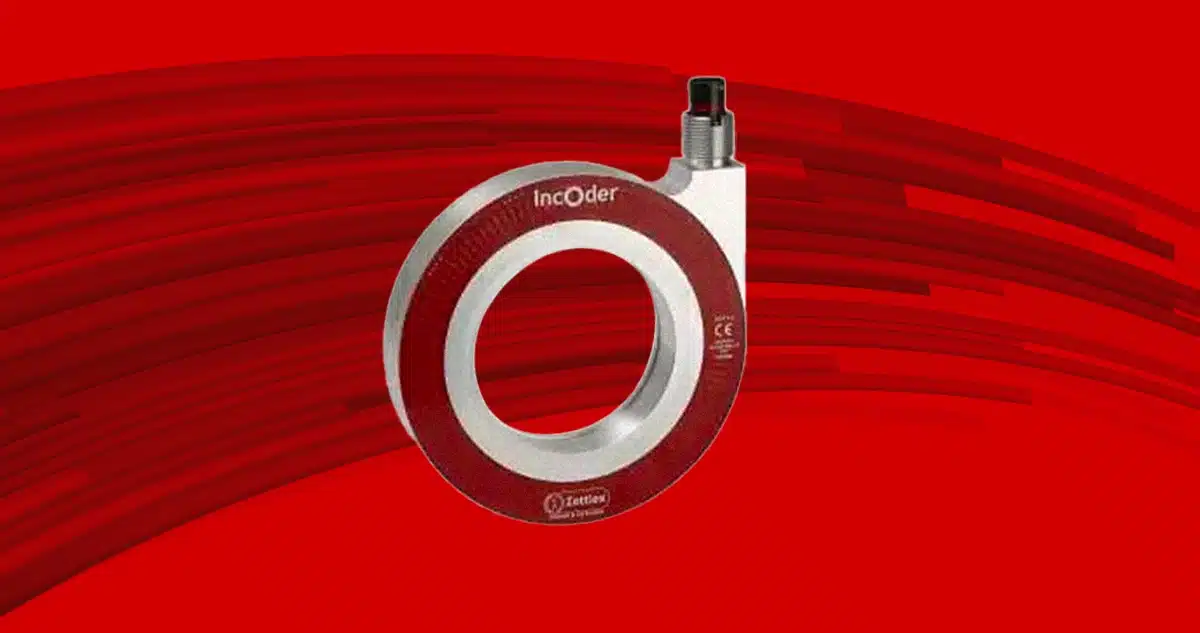
Parlare al giorno d’oggi di motori diretti, o direct drive, è in molti settori dell’automazione industriale una tecnologia assodata mentre questa tipologia di motorizzazioni trova sempre più ampio impiego anche in campi fino ad oggi riservati a sistemi più tradizionali. Questo articolo confronta le possibili soluzioni cercandone i vantaggi e i punti critici.
Terminologia
Teoricamente il termine motore diretto o direct drive può essere applicato a qualsiasi motore a cui venga applicato direttamente il carico senza altri elementi di trasmissione quali ingranaggi, pulegge, catene, riduttori. Solitamente si riferisce all’impiego di motori sincroni a magneti permanenti brushless, che trasmettono direttamente la loro coppia al carico. Spesso si sviluppano lungo il diametro, contenendone contemporaneamente l’altezza e caratterizzati da un foro passante. Vengono individuati come motori coppia e sviluppano una coppia costante a tutte le velocità, sino alla nominale.
Come funziona un direct drive?
I motori diretti funzionano in modo simile ai motori brushless. I magneti sono collegati al rotore mentre gli avvolgimenti sono disposti sullo statore del motore. Quando gli avvolgimenti sono energizzati, producono un campo magnetico che attira o respinge i magneti del rotore provocandone una rotazione controllata. Esistono sia direct drive rotativi che lineari.
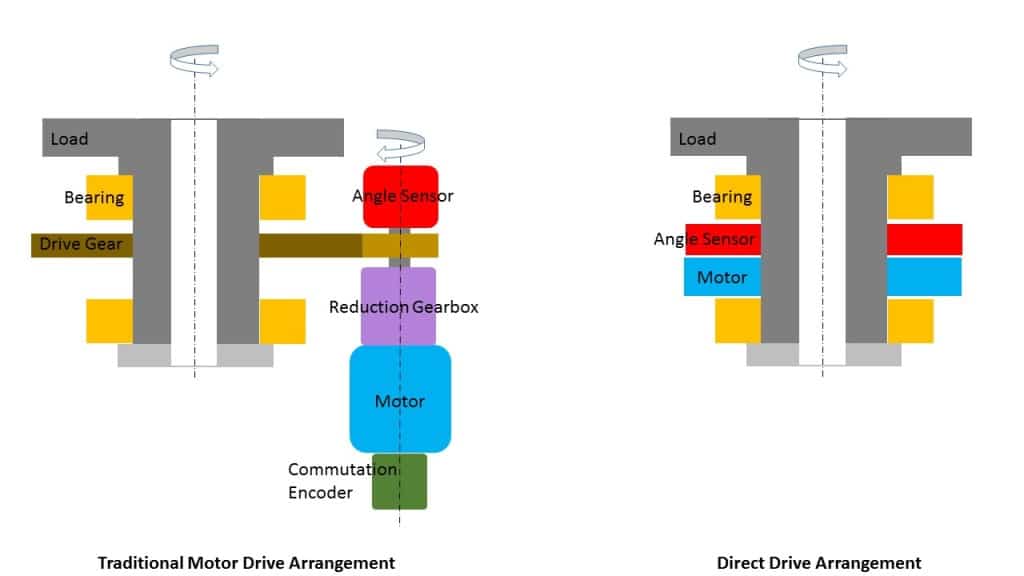
I motori diretti hanno solitamente un numero elevato di poli (>20 e talvolta > 100); sono disponibili motori torque da 1 mt di diametro, in grado di produrre coppie sino a 10 KNm. Molti si presentano come frameless ovvero senza alloggiamento e senza cuscinetti e sensore di retroazione. Questo permette ai costruttori di macchine, o agli integratori, di semplificare la loro struttura di alloggiamento, di dimensionare in proprio l’albero e i cuscinetti ottimizzandone la forma, le dimensioni, il peso e le prestazioni dinamiche.
Il rapporto coppia/inerzia è più elevato rispetto ai tradizionali motori brushless, inoltre presentano una bassa costante elettrica. Ciò significa che la coppia viene applicata rapidamente quando si applica tensione raggiungendo un’ottima rigidità del sistema. I motori tradizionali sono progettati per generare coppia massima a velocità elevate, tipicamente oltre 1000 RPM, e dimensionati sulla potenza nominale. I motori torque sono invece normalmente dimensionati sulla coppia massima e continua anziché sulla potenza.
Pro e contro
I maggiori vantaggi dell’impiego di motori diretti sono:
Elevata prestazione dinamica e accuratezza nel controllo della posizione e della velocità
- Assenza di giochi e usura
- Elevata affidabilità: non essendoci parti meccaniche come ingranaggi, pulegge, guarnizioni, cuscinetti
- Compattezza: sviluppandosi sul diametro hanno un’altezza minore e dispongono di un foro centrale
- Altro rapporto coppia/inerzia e altro rapporto tra coppia e massa del motore diretto
- Basso ripple (cogging) di coppia
- Alta coppia a bassi giri
- Alta efficienza energetica: dovuta alla mancanza di elementi meccanici aggiuntivi
- Bassa rumorosità e basse vibrazioni autoindotte
- Assenza di manutenzione.
- Bassi consumi per raffreddamento: vista la geometria meccanica particolarmente favorevole
- Traferro relativamente grande: con buona resistenza agli urti e ottima soluzione in ambienti polverosi
Le ragioni che spingono un progettista a scegliere un motore diretto sono le possibili prestazioni ottenibili e una maggiore dinamica rispetto a soluzioni tradizionali. Soprattutto disporre di un foro passante è una soluzione per fare passare collettori elettrici, tubi pneumatici, cavi elettrici.
Lo svantaggio principale è spesso più percepito che reale; i direct drive sono a volte considerati più costosi dei motori tradizionali. Spesso è vero se paragoniamo semplicemente il costo delle motorizzazioni ma, una più attenta e ampia valutazione che tenga conto delle parti meccaniche che vengono eleminate, della semplificazione meccanica complessiva, della riduzione di manutenzione ne fanno, anche economicamente, una soluzione vincente. Inoltre il costo dei motori diretti sta gradualmente diminuendo, anche grazie alla disponibilità di magneti al neodimio ferro boro (Nd-Fe-B) più potenti e all’aumento esponenziale avuto nell’utilizzo di queste motorizzazioni. Un esempio tipico lo troviamo in applicazioni molto sensibili ai costi come le lavatrici in cui i motori tradizionali stanno per essere soppiantati dall’impiego di motori torque, eliminando cinghie e pulegge, rendendo la trasmissione del moto più silenziosa e affidabile. Le maggiori applicazioni di motorizzazioni dirette si possono trovare nelle macchine utensili CNC, nei sistemi di confezionamento, nella robotica, nei sistemi radar, in ambito militare, nelle telecomunicazioni, nelle tavole rotanti, nei telescopi. La gamma è sempre più ampia ed è prevedibile un ulteriore ampliamento nel prossimo futuro.
La maggior parte dei motori tradizionali presenta intrinsecamente un forte cogging di coppia ma, vista l’elevata velocità di esercizio, questo effetto risulta nella maggioranza dei casi irrilevante sulle prestazioni finali. I direct drive possono soffrire di questo inconveniente in modo più accentuato a meno di impiegare dei feedback con maggiore risoluzione. È sicuramente uno dei punti che ha rallentato l’impiego di queste nuove motorizzazioni, dovendo impiegare dei controlli più sofisticati per il comando degli stessi.
Ma anche nel campo dei controllori sono stati fatti notevoli implementazioni arrivando a tempi di campionamento maggiori di 4 KHz a costi accessibili.
Uno dei maggiori vantaggi dei motori torque è la trasmissione diretta e una maggiore precisione nel posizionamento, nel controllo della velocità e della dinamica. Invece di collegare il carico con un giunto, con catene o cinghie, con ingranaggi o pulegge un motore diretto si flangia al carico; non ci sono isteresi, giochi, movimenti persi qualsiasi sia la direzione del posizionamento. Ma questi vantaggi sono possibili solo in presenza di un dispositivo di retroazione ad alta risoluzione. I sensori di Hall, tipicamente impiegati per la commutazione di potenza, non offrono prestazioni adatte per consentire un posizionamento preciso e un adeguato controllo della velocità.
Se il foro del motore diretto è sufficientemente piccolo, inferiore a 50 mm, vi è un’ampia gamma di feedback basati su tecnologia ottica, magnetica o induttiva. Poiché la maggior parte dei sensori di posizione hanno una forma costruttiva che dispone di un piccolo albero di ingresso, questo ha comportato un problema nell’integrazione dei motori torque.
La prima opzione è di impiegare un encoder ottico, con alimentazione DC e uscita digitale assoluta o incrementale. Non sono adatti per ambienti con polveri o con liquidi, che comprometterebbero la generazione corretta dei segnali. Inoltre le tolleranze molto ristrette, gamma di temperatura di impiego ristretta, forte sensibilità a shock ne limitano l’impiego. Gli encoder capacitivi possono superare queste problematiche ma le possibili scariche elettrostatiche diventano un limite. Gli encoder magnetici hanno una precisione bassa a causa dell’isteresi magnetica e sono inoltre molto sensibili ai campi magnetici generati dal motore. La più tradizionale soluzione rimane l’impiego di resolver che danno una forte affidabilità e sicurezza applicativa, soprattutto in ambito aerospaziale e della difesa. Tuttavia sono molto ingombranti, pesanti e costosi, soprattutto quando dispongono di fori passanti superiori a 50 mm.
Un nuovo approccio
Una nuova tipologia di sensore di posizione viene sempre più impiegata come feedback dei motori torque, si tratti di sensori induttivi o incOders. Usano lo stesso principio elettromagnetico o induttivo dei resolver, ma invece degli avvolgimenti di trasformazione ingombranti, utilizzano circuiti stampati laminati, quindi meno costosi, più compatti e più leggeri. Invece dei complessi circuiti di alimentazione e elaborazione di segnali AC richiesti dai resolver, gli incOders utilizzano semplici interfacce elettriche simili a quelle impiegate dagli encoder ottici, alimentazione in DC e uscita digitale.
Gli incOders sono disponibili in formati assoluti o incrementali, segnali A e B, con risoluzioni fino a 22 bit, circa 4 milioni di conteggi per giro. Accuratezza inferiore a 40 arc-secondi, ovvero 0,01 ° e coefficiente di dilatazione termica molto bassa, inferiore a 0,5 ppm/K. Sono state migliorate le prestazioni dinamiche grazie alla possibilità di raggiungere velocità di rinfresco di 10 KHz. Anche costruttivamente sono l’ideale applicativo con un diametro largo, un profilo molto basso, un grande foro passante. Possono essere fissati meccanicamente al motore diretto senza ulteriori parti meccaniche come cuscinetti o guarnizioni o giunti.
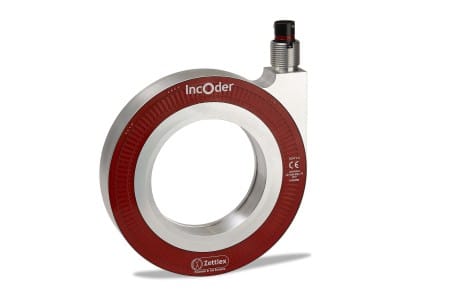
La combinazione di incOders e motori torque è sempre più preferita da molti integratori, i risultati ottenuti confermano che permettono di controllare i posizionamenti in modo altamente affidabile, dinamico e preciso anche per sistemi in ambiente medicale, aerospaziale, industriale e petrolchimico.