Questo documento è per ingegneri, tecnici e studenti – pensato specialmente per chi ha bisogno, in poco tempo, di apprendere le basi su controllo di posizione […]
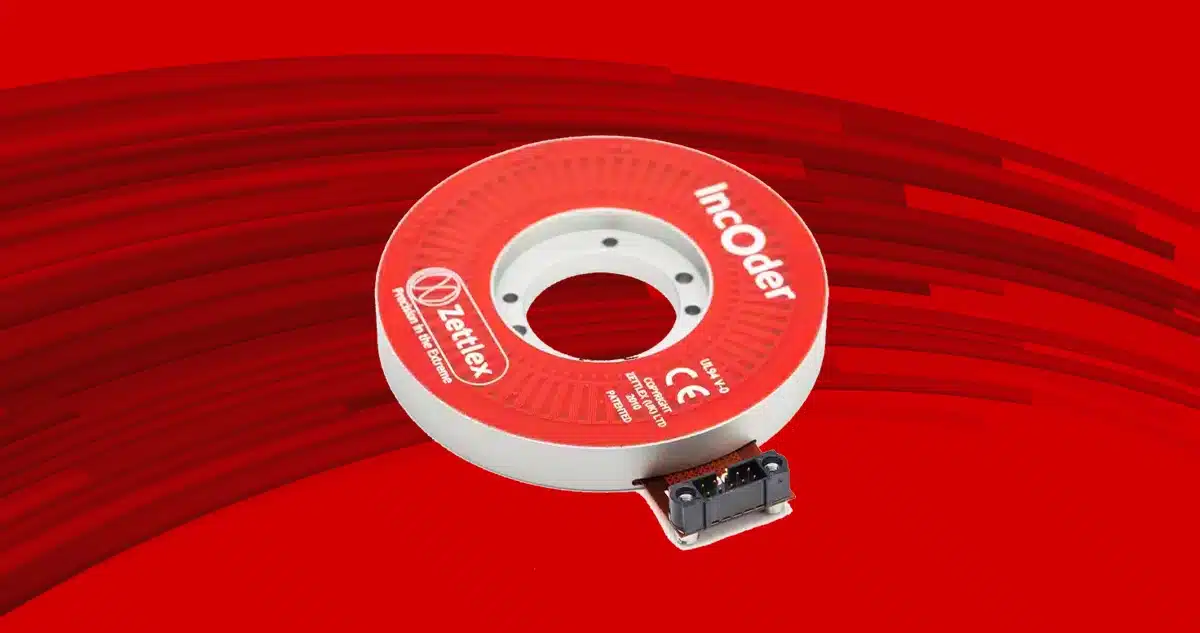
Questo documento è per ingegneri, tecnici e studenti – pensato specialmente per chi ha bisogno, in poco tempo, di apprendere le basi su controllo di posizione e sensori di posizione. Il documento è deliberatamente sintetico e mira a dare una visione d’insieme piuttosto che trattare l’argomento approfonditamente.
Terminologia
Noi ingegneri amiamo i tecnicismi – questo ci aiuta a differenziarci dai comuni mortali. Sfortunatamente, un lessico eccessivamente tecnico rende poco comprensibile, per un ingegnere specializzato in un’area, affrontare tematiche proprie di un’altra. Il controllo di posizione non fa eccezione, iniziamo quindi a fare un po’ di chiarezza con la terminologia.
Ingannevolmente, alcuni sensori, solitamente sensori di prossimità, sono in effetti switch di prossimità dal momento in cui determinano la presenza o l’assenza di un oggetto. Questo vuol dire che generano un semplice output digitale on/off invece che una misurazione continua della posizione. In questo documento, ci focalizzeremo su tipologie di sensori vere e proprie e non sugli switch. In altre parole, sensori che generano un segnale (solitamente elettrico) commisurato ad un posizionamento lungo un range di misura.
Deceptively, some sensors, usually proximity sensors, are proximity switches from the moment they determine the presence or absence of an object. This means they generate a simple digital on/off output instead of a continuous position measurement. This paper will focus on true sensor types and not switches. In other words, sensors that generate a signal (usually electrical) commensurate with positioning along a measurement range.
Ci sono anche altri termini che si riferiscono alla posizione (lineare e rotativa): dislocazione, angolo, posizione angolare, rotazione, rotativo, lineare – ancora una volta, per le finalità di questo documento, useremo il termine generico “posizione” per coprire geometrie sia lineari sia angolari.
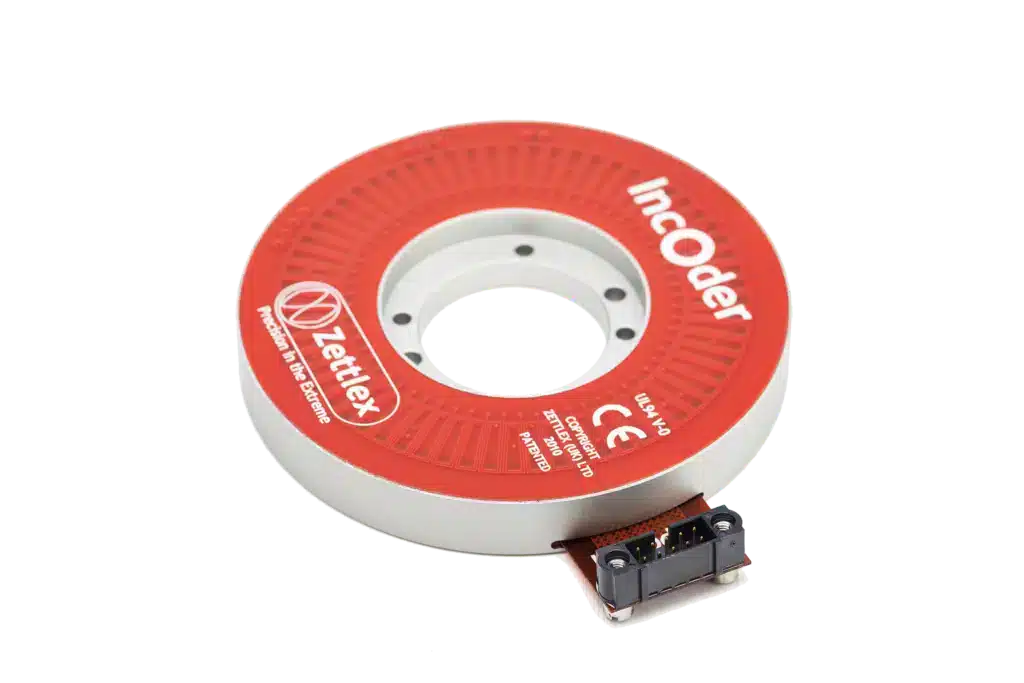
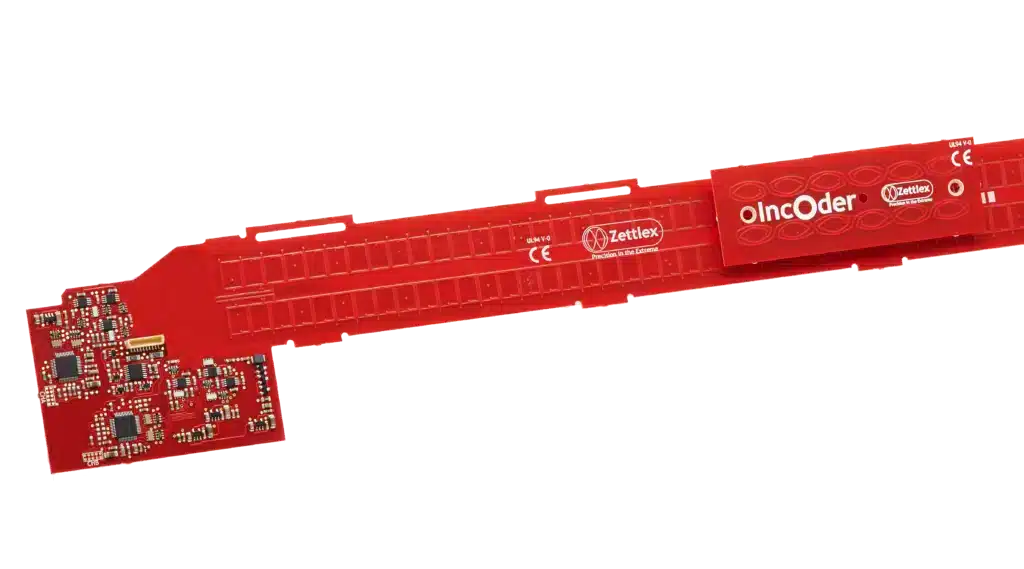
Quasi tutti i sensori di posizione, possono inoltre essere considerati come sensori di velocità. Dal momento in cui la velocità si può definire come rapporto tra lo spazio percorso e il tempo impiegato a percorrerlo, allora, ogni sensore di posizione la cui posizione è aggiornata frequentemente è, di fatto, anche un sensore di velocità. La velocità può essere determinata facilmente da tipici sistemi di controllo moderni differenziando l’output del sensore in relazione al tempo o, più semplicemente, contando le variazioni di posizione rispetto al tempo.
Tutti i sensori di posizione possono essere classificati come assoluti o incrementali. L’output generato da un sensore incrementale cambia al variare della posizione. Contrariamente, i sensori assoluti producono un segnale che è proporzionale alla posizione reale sia ferma sia in movimento. Un test efficace per determinare se un sensore è assoluto o incrementale è osservare cosa succede all’accensione. Se c’è un segnale di posizione reale senza alcun movimento, allora il sensore in questione è un sensore assoluto.
Basi sulla misurazione della posizione
Forse, il giorno che hanno fatto teoria della strumentazione non eri a lezione; quando hanno spiegato accuratezza, risoluzione, ripetibilità e tutte quelle cose. Non ti preoccupare, sei in buona compagnia. Molti ingegneri hanno dimenticato oppure mai veramente compreso questo argomento. La terminologia e i – piuttosto esoterici – concetti tecnici applicati alla strumentazione sono confusi. Ciò nonostante, questi sono importanti per selezionare il sensore di posizione più adatto alla tua applicazione. Sbaglia questa scelta e potresti trovarti a pagare molto di più del dovuto per i tuoi sensori di posizione; sbaglia nell’altro senso e il tuo prodotto o sistema di controllo potrebbe mancare di performance fondamentali. Per iniziare, alcune definizioni:
- L’accuratezza di un sensore è la misura dell’esattezza del suo output
- La risoluzione è la misura del più piccolo incremento o decremento di posizione misurabile dal sensore.
- La precisione è il grado di ripetibilità del sensore
- La linearità è la differenza tra l’output e la posizione effettiva misurata dal sensore.
Per capire la differenza tra accuratezza e precisione possiamo utilizzare l’analogia di una freccia tirata su un bersaglio. L’accuratezza descrive quanto la freccia è vicina al centro.
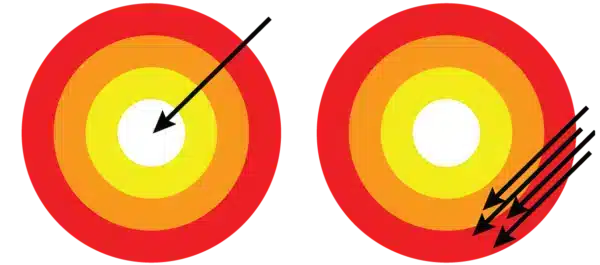
Se venissero lanciate molte frecce, la precisione equivarrebbe alla dimensione del raggruppamento delle frecce. Se tutte frecce sono raggruppate insieme, il gruppo è considerato preciso o, in altre parole, molto ripetibile. Un sensore di posizione perfettamente lineare è anche molto accurato. Per molte applicazioni, la linearità può essere considerata come equivalente all’accuratezza. Quindi è tutto chiaro, basta mettere a specifica dei sensori molto accurati e risolvi ogni problema. Sfortunatamente, questo approccio presenta alcune criticità. Primo, i sensori ad elevata accuratezza sono molto costosi. Secondo, i sensori ad elevata accuratezza richiedono un’installazione molto attenta il ché potrebbe non essere agevole per via di vibrazioni, espansione termica differente o, più probabilmente, per i costi che ne derivano. Terzo, alcuni tipi di sensori ad elevata accuratezza sono delicati e potrebbero soffrire di malfunzionamento o avarie se esposti ad ambienti ostili.
La strategia ottimale è di specificare quanto necessario – niente di più, niente di meno. Per esempio, per un sensore di posizione di un flussometro industriale, la linearità non sarà un requisito fondamentale dal momento in cui è probabile che le caratteristiche del flusso del fluido siano squisitamente non lineari. Più verosimilmente, sarà importante la ripetibilità al variare delle condizioni ambientali. Va notato che, in molte applicazioni, risoluzione e ripetibilità sono spesso più importanti della linearità.
In una macchina utensile a controllo numerico (CNC), ad esempio, è presumibile che sia l’accuratezza sia la precisione siano requisiti chiave. Di conseguenza, un sensore di posizione con elevata accuratezza (linearità), risoluzione ed elevata ripetibilità, saranno requisiti fondamentali anche in ambienti sporchi e umidi e senza interventi di manutenzione per lunghi periodi di tempo.
Tipologie comuni di sensori di posizione
I sensori di posizione sono impiegati in una grande varietà di applicazioni industriali e commerciali, da applicazioni aerospaziali e per la Difesa fino ad applicazioni low-cost quali automotive ed elettrodomestici. In effetti, subito dopo la misurazione della temperatura, nella nostra vita, la misurazione della posizione è la seconda proprietà più importante da misurare. C’è una stupefacente varietà di sensori di posizione tra cui scegliere al giorno d’oggi, ma come si sceglie quello giusto? Questa sezione delinea le principali tipologie di sensori analizzandone principali debolezze e punti di forza.
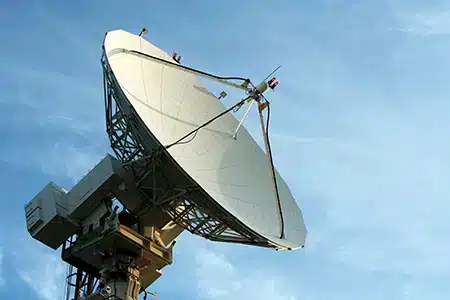
Potenziometri
Nonostante il trend verso i sensori contactless, i potenziometri (pots) rimangono i sensori di posizione più comuni. Questi, misurano una caduta di tensione in corrispondenza dello spostamento dei contatti elettrici lungo la traccia resistiva; ne consegue che la posizione è proporzionale alla tensione in uscita. I potenziometri sono disponibili in forme rotative, lineari o curvilinee e sono solitamente compatti e leggeri e variano da qualche centesimo per le versioni più semplici fino ad arrivare a 200$ per le versioni ad elevata precisione. Linearità inferiori a 0.01% sono possibili attraverso la rifilatura laser della traccia resistiva.
I potenziometri sono particolarmente indicati per applicazioni con cicli d’utilizzo modesti, ambienti gentili e performance rilassate. Sfortunatamente, i potenziometri sono sensibili ad usura, specialmente in ambienti con elevate vibrazioni e/o con particelle estranee come polvere e sabbia che a lungo andare abraderebbero la traccia resistiva. Dispositivi di qualità più elevata stimano la durata in termini di numero di cicli, ma spesso si trascurano gli effetti delle vibrazioni.
Deve essere inoltre tenuto in considerazione che i datasheet dei potenziometri spesso dichiarano “risoluzioni infinite”. Se questo è vero in linea teorica, dal momento in cui molti sistemi di controllo richiedono informazioni digitali, la risoluzione effettiva sarà quella data dal convertitore da analogico a digitale (il quale deve essere incluso tra le voci di costo).
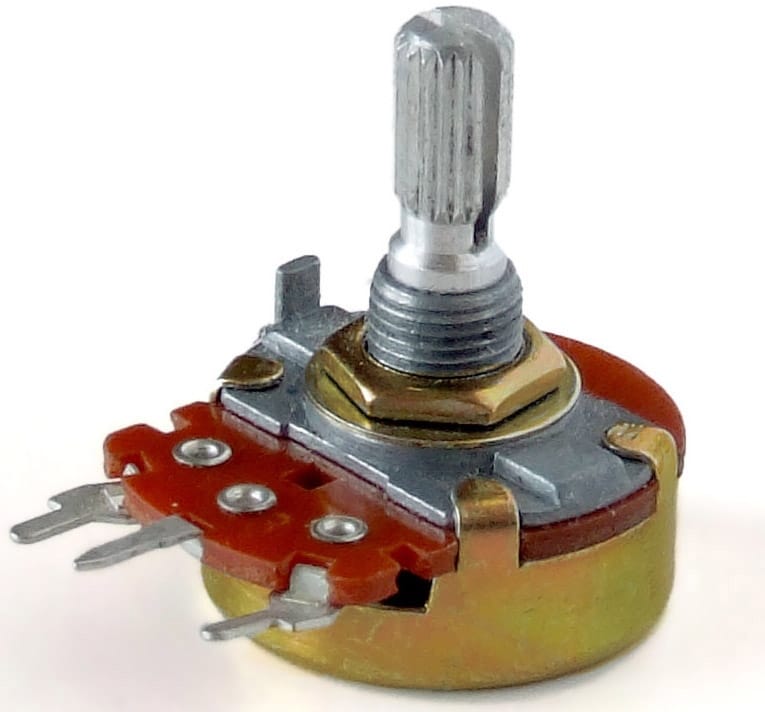
Stranamente, i potenziometri vengono classificati come “dispositivi semplici” in alcune applicazioni relative alla sicurezza in ambito aerospaziale, medicale e petrolchimico. Questo significa che pur essendo soggetti a diversi tipi di guasti, essi non sono soggetti alla stessa progettazione rigorosa e controllo da parte degli organismi di certificazione dei sensori elettrici. È una stupida ma reale situazione che rende difficile la sostituzione di potenziometri inaffidabili in alcune applicazioni.
Punti di forza: basso costo, semplici, compatti, leggeri, possono essere resi accurati Punti di debolezza: usura, vibrazioni, corpi estranei, temperature estreme
Ulteriori approfondimenti:
Sensori Ottici
I sensori ottici vengono solitamente chiamati encoder e sono una forma comune di sensori di posizione che variano da semplici dispositivi dal costo di qualche euro fino a sensori di precisione che possono arrivare a 10,000 euro. Tutti questi dispositivi sono accumunati dallo stesso principio: un fascio di luce è puntato attraverso o sopra un reticolo (grating), la luce derivante viene misurata con un foto-rilevatore e di conseguenza un segnale di posizione viene generato.
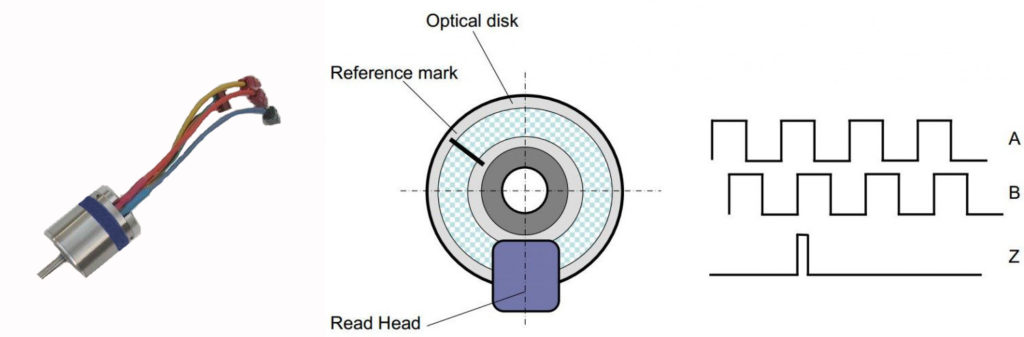
Gli encoder rotativi sono ampiamente disponibili, tipicamente con 50-50.000 count/giro e sono testati per funzionare bene in applicazioni in ambienti normali. Tuttavia, in ambienti più severi, se le lenti o il sistema di grating viene oscurato da particelle esterne come terra, trucioli o acqua, non sarà possibile effettuare la misurazione.
Nella selezione di un sensore ottico, è importante sapere che se il valore citato del sensore è 1,000 count/giro, questo non vuol dire che l’accuratezza sia 1/1000th / giro. È importante inoltre leggere attentamente il datasheet del sensore, specialmente con kit di montaggio e dischetti che richiedono estrema precisione in fase di assemblaggio per evitare contaminazioni. Se l’encoder ha un disco di vetro, il dispositivo avrà una resistenza limitata a shock e vibrazioni.
Punti di forza: elevata risoluzione, elevata accuratezza se assemblato correttamente, ampiamente disponibile Punti di debolezza: corpi esterni, guasti catastrofici senza preavviso, shock, temperature estreme.
Approfondimenti:
Sensori Magnetici
Tutti i sensori magnetici utilizzano un principio di misura simile: quando un magnete si muove in relazione ad un ricettore magnetico, il campo magnetico cambia in proporzione al loro spostamento relativo. Una forma comune sono i sensori di Hall, disponibili in chip. Sono spesso utilizzati per automotive e applicazioni con motori elettrici che richiedono performance di misurazione modeste.
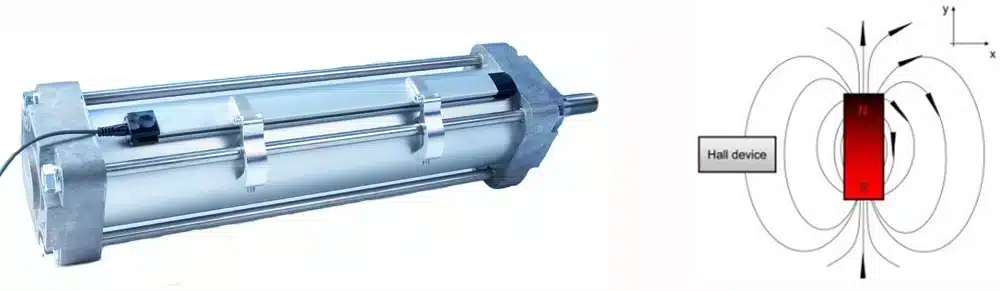
Grazie alla tolleranza ai corpi esterni, i sensori magnetici risolvono molte delle problematiche che si possono incontrare con i dispositivi ottici. Ciò nonostante, questi sensori vengono impiegati raramente per applicazioni richiedenti elevata accuratezza, a causa dell’isteresi magnetica e la necessità di avere una meccanica di precisione tra la parte in rotazione e quella statica. Ogni datasheet deve essere letto attentamente nelle parti relative a tolleranze di installazione, coefficiente di temperatura e temperatura operativa.
Un’ulteriore considerazione è la prossimità dei materiali magnetici o cavi elettici. I magneti potrebbero infatti attrarre particelle estranee e una delle cause di guasto è proprio l’accumulo nel tempo di materiali quali trucioli e particelle. Solitamente, i sensori magnetici non rappresentano la prima scelta per applicazioni in ambienti ostili o condizioni di shock a causa della nota fragilità dei nuovi magneti al neodimio (NdFeB).
Punti di forza: discretamente robusti, la maggior parte dei liquidi non hanno effetto Punti di debolezza: temperatura, isteresi, meccanica di precisione, fonti vicine di ferro e DC, fonti in DC e basse performance per impatti e shock. Approfondimenti:
Approfondimenti:
Sensori Magnetostrittivi
Questi sensori utilizzano un fenomeno poco comune, presente in alcuni materiali, chiamato magnetostrizione. Quando un magnete arriva in prossimità di un materiale, fa sì che l’energia passi attraverso il materiale da riflettere. La posizione può essere calcolata dal momento in cui riceve un impulso di energia per spostarsi avanti e indietro su una striscia di materiale magnetostrittivo – solitamente un cavo sottile o una striscia.
Quasi tutti i sensori magnetostrittivi sono lineari perché la delicata striscia magnetostrittiva va tenuta in un “involucro” quale un estruso di alluminio. Questa protezione fa sì che i dispositivi magnetostrittivi non temano usura o problematiche legate alla durata e che possano essere utilizzati in applicazioni ad altra pressione come, ad esempio, i martinetti idraulici. Ogni sensore deve essere calibrato dal costruttore e questo, combinato all’housing di precisione, rende i sensori magnetostrittivi relativamente costosi. Questa tecnica è inoltre sensibile ad ogni altro disturbo durante il tempo di volo (TOF), solitamente la temperatura. I datasheet dei magnetostrittivi, solitamente stimano l’accuratezza a temperatura costante, gli ingegneri dovranno quindi considerare questo aspetto usando i coefficienti di temperatura stimati. Il sottile materiale magnetostrittivo è delicato e l’assemblaggio su entrambe le estremità è un’operazione critica. Tirando le conclusioni, possiamo dire che i sensori magnetostrittivi non dovrebbero essere scelti per ambienti severi o con vibrazioni.
Punti di forza: robusti, ottimi per impiego ad altra pressione, la percentuale di accuratezza migliora con la lunghezza Punti di debolezza: abbastanza costosi, shock. Effetti dovuti al variare della temperatura, inaccurati sulle brevi distanze (<100mm). Approfondimenti:
Approfondimenti:
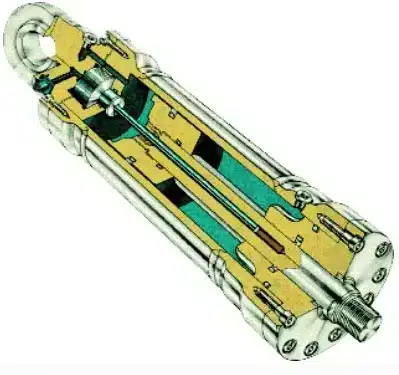
Sensori Capacitivi
Un condensatore è un dispositivo elettronico in grado di accumulare carica. Tipicamente, presenta due piastre conduttive separate da un isolante. La quantità di carica che il condensatore può immagazzinare varia in relazione alla dimensione delle piastre, la percentuale della loro sovrapposizione, la distanza e la permeabilità del materiale tra le piastre. Nella sua forma più semplice, un sensore di posizione capacitivo, misura la distanza tra le piastre. Lo sfasamento è tipicamente nell’ordine di grandezza di 1mm per la misurazione di carico, sforzo e pressione.
Un’altra forma viene utilizzata per sensori di posizione nelle quali una serie di piastre vengono tagliate o incise lungo l’asse di misura. Nel momento in cui un’altra piastra si muove perpendicolarmente, la capacità dei circuiti attraverso gli assi varia indicando le posizioni relative delle due parti. I sensori di posizione capacitivi sono poco comuni e usati raramente in applicazioni legate alla sicurezza. Sfortunatamente, come la sovrapposizione delle piastre ecc., la capacità cambia anche con temperatura, umidità, materiali limitrofi e corpi estranei, i quali rendono sfidante la progettazione di un sensore di posizione stabile e molto accurato.
Abbiamo lavorato su sensori, automazione ed elettronica per quasi 30 anni. Dobbiamo ancora incontrare un ingegnere progettista che sia contento di aver scelto un sensore di posizione capacitivo. I sensori capacitivi hanno una pessima reputazione tra ingegneri esperti ed è improbabile che vengano scelti per applicazioni legate alla sicurezza. Alcuni produttori hanno smesso di parlare di “capacitivi”, preferendo termini alternativi come charge storage, charge coupling o effetti elettrici su materia offuscata. Non va bene. Ci sono così tante cose che possono andare storte che è meglio evitarli a meno che tu non abbia bisogno di elevate accuratezza di misura in applicazioni molto stabili e in condizioni ambientali controllate.
Punti di forza: compatti, bassa potenza Punti di debolezza: elevati coefficienti di temperatura e umidità, sensibili a materiali estranei, tolleranze limitate in installazione Approfondimenti:
Approfondimenti:
Induttivi tradizionali
I sensori tradizionali di posizione basano il loro funzionamento su principi di induzione e sono stati utilizzati per più di 100 anni. Hanno un’eccellente reputazione per operazioni sicure ed affidabili in condizioni difficili il ché li rende una scelta quasi obbligatoria in molte applicazioni legate alla sicurezza.
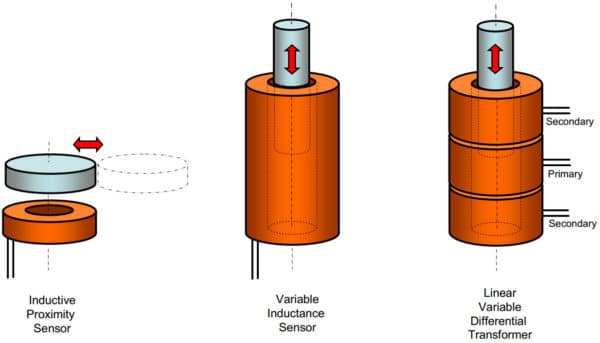
I sensori di posizione lineari vengono solitamente appellati come trasformatori a riluttanza variabile o Linear Variable Displacement Transducer (LVDT). Le varianti rotative sono conosciute come synchros, resolver o RVDT. Gli LVDT usano una costruzione una particolare configurazione del trasformatore con almeno tre bobine: uno primario e due secondari. Il rapporto del segnale indotto indica la posizione dell’asticella relativa alla bobina. Questa tecnica rapporto-metrica è la chiave dell’elevato grado di stabilità e delle prestazioni di misura dell’LVDT. Mentre i sensori ottici e magnetici richiedono circuiti elettrici adiacenti al punto di rilevamento, i sensori a induzione posso dislocare l’elettronica lontano dal punto di rilevamento, il ché permette di posizionare il sensore in ambienti ostili e l’elettronica in ambienti più benevoli. Ad ogni modo, a causa della costruzione dell’avvolgimento del trasformatore, tendono ad essere grossi, ingombranti e costosi
Punti di forza: elevata accuratezza, affidabilità, ambienti estremi, largamente disponibili Punti di debolezza: costosi, ingombranti, pesanti Approfondimenti:
Approfondimenti:
Nuova generazione di induttivi o IncOder
La nuova generazione di sensori induttivi – spesso definiti come IncOder – usano lo stesso principio dei tradizionali sensori induttivi, quindi offrono buone performance di misura senza contatto in ambienti severi. Tuttavia, invece che usare ingombranti bobine di avvolgimento, questi sensori usano circuiti stampati su substrati flessibili o rigidi.
Il passaggio ad avvolgimenti stampati porta altri vantaggi:
- Una significativa riduzione dei costi di produzione, dimensione e peso
- Maggior flessibilità nella forma
- Eliminazione di fonti di inaccuratezza proprie del processo di avvolgimento
- Complesse geometrie di misura come rilevamento di posizione curvilineo, 2D e 3D
- Possono essere posizionati sensori multipli nello stesso posto usando una scheda multistrato (es: sensori ridondanti in applicazioni legate alla sicurezza)
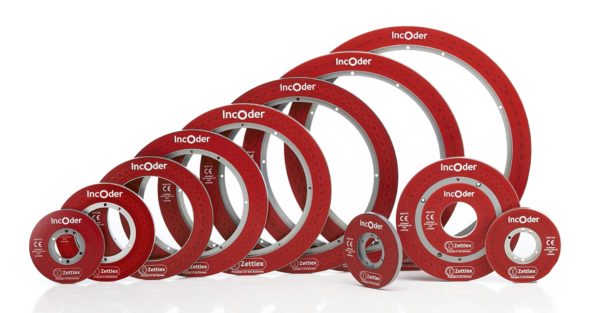
Solitamente, le performance dell’EMC sono tanto buone tanto quelle dei resolver o degli LVDT. Questo è evidenziato dai dispositivi induttivi di nuova generazione per il settore aerospaziale e della difesa.
Punti di forza: elevata accuratezza, affidabilità, robustezza, Punti di debolezza: più costosi dei potenziometri
Approfondimenti:
Errori comuni
La lista seguente elenca gli errori più comuni che gli ingegneri fanno in relazione ai sensori di posizione:
Non tenere in considerazione i costi di un guasto al sensore. Tutti gli ingegneri voglio scegliere una soluzione low cost. Questo però non vuol dire scegliere semplicemente il sensore più economico. Come regola generale, il costo del guasto di un sensore sul campo, è destinato ad essere un problema maggiore e spesso più costoso di un sensore di posizione.
In altre parole, a conti fatti, selezionare un sensore che non si guasti sul campo risulterà essere sempre la scelta migliore in termini economici. Inoltre, c’è sempre la natura del guasto da tenere in considerazione. Un sensore che non funziona correttamente e che si arresta, è solitamente meglio di un sensore in avaria che produce una lettura sbagliato ma credibile. Le conseguenze di una lettura sbagliata in termini di costo e sicurezza, possono essere addirittura superiori di quelle di un sensore che semplicemente smette di funzionare o che ti da un errore.
Non capire la differenza tra ripetibilità, risoluzione e accuratezza. Rileggi la sezione 3 e assicurati di aver compreso le basi. È importante evitare l’errore (spesso diffuso dalla stessa industria dei sensori di posizione) di confondere risoluzione e accuratezza. Solo perché un encoder produce un milione di counts/giro, non vuol dire che esso sia accurato per un milionesimo di rivoluzioni. Al contrario, in molte applicazioni, spesso il requisito chiave è la ripetibilità e quindi, non è necessario mettere a specifica sensori con elevata accuratezza (=costi elevati).
Combinazione errata sensore-ambiente. L’uomo ha trovato diversi modi per sfruttare la maggior parte dei fenomeni fisici base per misurare la posizione attraverso l’utilizzo di tecniche ottiche, magnetiche, capacitive, resistive e induttive. Ogni tecnica ha la sua propria forza e debolezza. Come regola generale, non scegliere:
- Sensori resistivi (potenziometrici), ottici o capacitivi per ambienti sporchi o umidi. Condensazione e ghiaccio superficiale in attrezzatura all’aperto sono una delle cause principali di avaria.
- Sensori ottici, magnetici o capacitivi con applicazioni con range di temperatura esteso (la maggior parte non funzionerà sopra i 125°C).
- Sensori magnetici dove sono richieste performance ad elevate prestazioni, a meno ché non sia anche possibile eliminare i campi magnetici e predisporre un supporto meccanico di precisione per il sensore.
- Potenziometri in applicazioni con vibrazioni forti o prolungate. Questo perché i suoi contatti striscianti elettrici sono soggetti a guasti e usura dati da microscopici movimenti indotti da un sacco di vibrazioni.
Derivare una misura invece che misurare direttamente. Nella progettazione di un sensore di posizione, è buona norma misurare la posizione dell’oggetto a cui si è interessati. In altre parole misurarne la posizione direttamente. Prova a non dedurre o calcolare la posizione di un componente attraverso la misurazione di un altro componente come potrebbe essere un ingranaggio alla fine della linea di trasmissione o la posizione di un motore. È probabile che ci sia gioco, spazi, variazione da parte a parte, guasto meccanico, dilatazioni termiche differenziali/contrazioni, ecc. che ne comprometterebbero inevitabilmente il grado di misura della performance e l’affidabilità.
Dimenticare cavi e connettori. Cavi e connettori sono una delle cause primarie di guasti al sensore. Assicurati che siano presi in considerazione in ogni progetto e soprattutto che siano sollevati da sforzi in tutte le applicazioni che incontrano movimento, shock e vibrazioni.
Non leggere le diciture in piccolo del datasheet. Quella dei sensori di posizione è un’industria competitiva. Sfortunatamente, questo ha portato alcuni produttori a tenere un atteggiamento un po’ troppo furbo con le specifiche tecniche. Spesso la fanno franca perché sanno che molti ingegneri non avranno letto un documento come questo. La conseguenza è che i sensori verranno pubblicizzati con, per esempio, una risoluzione di 10,000 count/rev – senza però indicare l’accuratezza. Un altro esempio, è un sensore con una risoluzione incredibilmente alta ma con molta meno ripetibilità – in altre parole, molta risoluzione ma anche un sacco di rumore in output. Il trucco è non farsi ingannare da numeri in evidenza nel datasheet – leggi le diciture in piccolo.
Come scegliere un sensore di posizione
Il primo, nonché più importante, passo per scegliere un sensore di posizione consiste nell’essere molto chiari sulle performance che si necessitano, con focus particolare sui valori di risoluzione, ripetibilità e linearità. Esagerare questi valori porterà alla selezione di un prodotto inutilmente costoso. Il trucco è trovare un sensore che calza a pennello per l’utilizzo che se ne deve fare al minor costo complessivo – ricordandosi, in fase di configurazione, di aggiungere una tolleranza per eventuali guasti sul campo.
Puoi usare la seguente check-list per assicurarti di aver preso in considerazione tutti gli aspetti importanti nelle tue specifiche. Fornire questi dati ad un costruttore di sensori di posizione insieme ad un disegno tecnico dell’ingombro, farà sì che si pongano le basi necessarie per la tua discussione:
- Geometria – per esempio, o lineare o rotativo o curvilineo o 2D o 3D
- Spazio dell’ingombro – punti di fissaggio meccanici, posa cavi e ingombri
- Tipo di misura – incrementale o assoluta
- Fondo scala – per esempio, 360 gradi o 600mm
- Risoluzione – in altre parole, la più piccola variazione che deve essere misurata – per esempio 0,1 gradi o 0,2mm
- Ripetibilità – in altre parole, la stabilità della misurazione in termini di ritornare allo stesso punto – ad esempio ripetibilità = +/- 0,025mm
- Linearità – lo scarto massimo consentito da una lettura perfettamente accurata. Faresti meglio a pensare attentamente a questo aspetto dal momento in cui ci siamo resi conto che spesso quel che conta veramente in molte applicazioni è la ripetibilità.
- Range di temperatura a riposo e di funzionamento – -40°C +85°C è il più comune
- Alimentazione elettrica – per esempio, 5V, 12V o 24V
- Output elettrico – ad esempio dati seriali, impulsi, 0-10V, 4-20mA
- Cose poco comuni – come – “vogliamo tenere il consumo energetico più basso possibile” oppure “è per immersione in acido solforico bollente” o ancora “stiamo utilizzando un dispositivo capacitivo e abbiamo problemi di affidabilità”.
Zettlex
Zettlex progetta e costruisce sensori per la precisa misurazione di posizione o velocità in ambienti difficili. I sensori di posizione sfruttano una tecnologia priva di contatto unica per la trasmissione di elevate accuratezza e affidabilità di misura in condizioni difficili. I nostri sensori di posizione induttivi vengono impiegati per servo controlli, servo motori e interfacce utente in ambito medicale, difesa, aerospaziale, industriale, marino, sport motoristici e pertrolchimico.