Dai dispositivi elettromeccanici, ai PLC di sicurezza, ai fieldbus, alle nuove sfide di Industry 4.0 Le macchine e i sistemi di automazione devono rispondere a norme […]
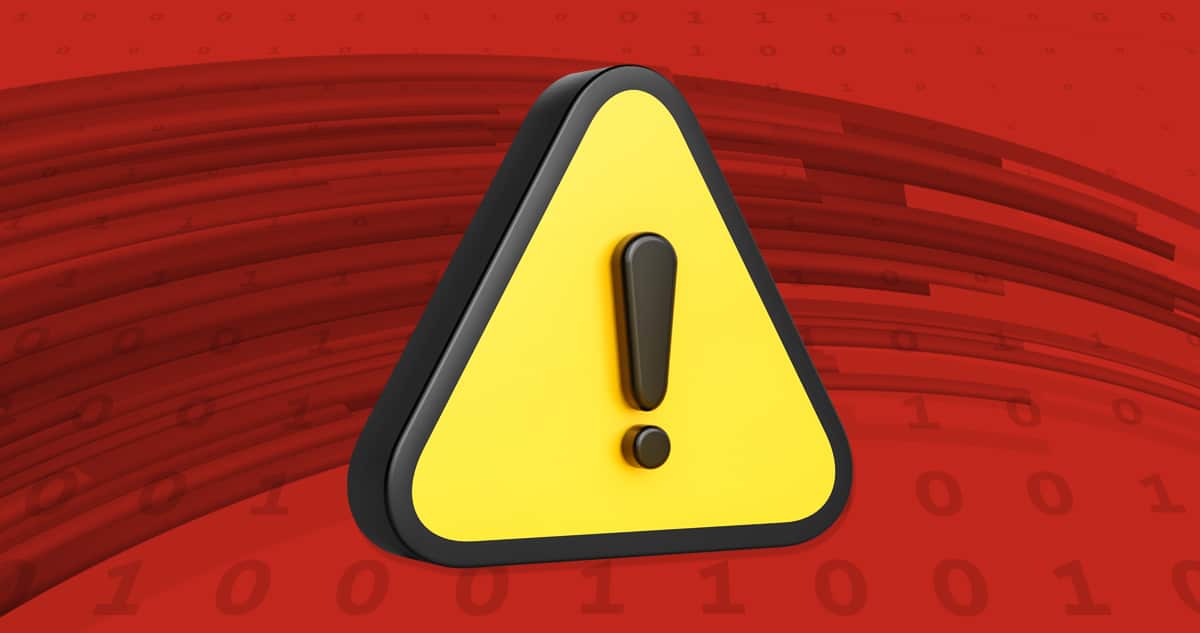
Dai dispositivi elettromeccanici, ai PLC di sicurezza, ai fieldbus, alle nuove sfide di Industry 4.0
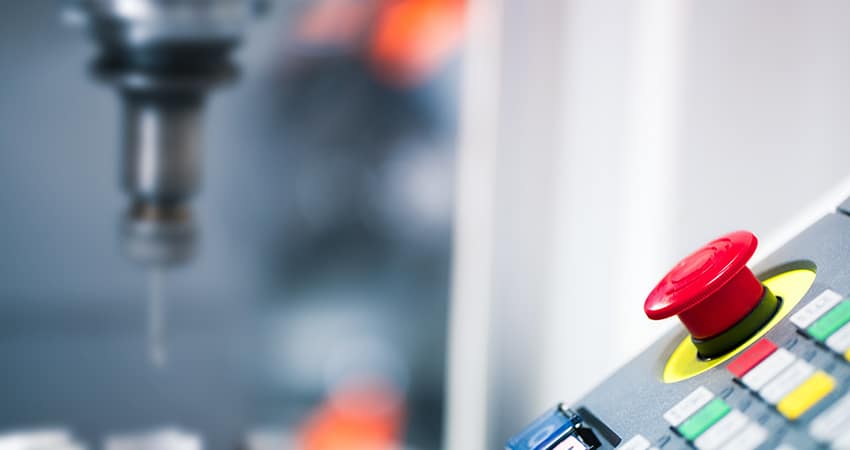
Le macchine e i sistemi di automazione devono rispondere a norme di sicurezza ormai comuni in tutto il mercato europeo. In passato, per garantire la rispondenza a tali norme si potevano utilizzare solo dispositivi elettromeccanici (come i relè di sicurezza), essendo vietate sia le soluzioni puramente elettroniche, sia quelle basate unicamente sul software. L’interruzione di un circuito elettrico, per esempio, era considerata accettabile solo se veniva ottenuta con un interruttore o un sezionatore che provocava una discontinuità fisica nel circuito stesso. La scelta dei componenti utilizzati per creare un sistema di sicurezza si è continuamente ampliata, fino a comprendere anche i dispositivi di interblocco, le barriere fotoelettriche, le pedane sensibili alla pressione, i pulpiti di comando a due mani e così via.
I PLC di sicurezza ‘sdoganano’ la tecnologia elettronica e l’informatica
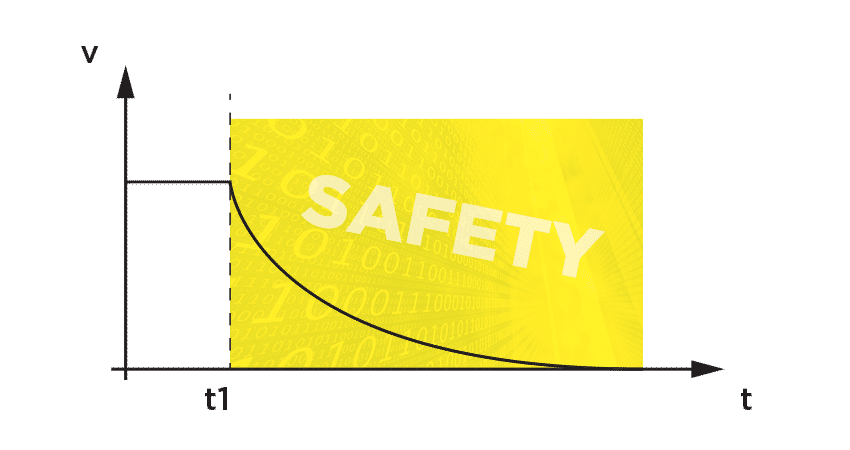
Negli ultimi anni, i segnali emessi dai dispositivi di sicurezza in campo vengono monitorati anche tramite componenti come i PLC di sicurezza: si tratta di PLC progettati con particolari criteri che riguardano sia il cablaggio degli I/O, sia l’elaborazione del programma di controllo per rispondere a quelli che sono i criteri di messa in sicurezza di una macchina, un impianto o un’area in generale. Spesso, per esempio, nel PLC di sicurezza vi sono due processori che eseguono un controllo di plausibilità sulla logica che vanno ad elaborare. Nel caso venga rilevata un’incongruenza, tutto si porta in una condizione di sicurezza. Esistono poi dei criteri che prevedono anche la verifica del tempo effettivo di elaborazione delle informazioni, perché ci deve essere una determinata reazione in termini di sicurezza quando, per esempio, si preme un pulsante di emergenza. Nel tempo, i PLC di sicurezza hanno attraversato una serie di trasformazioni simili a quelle dei PLC standard: dalle unità stand-alone, alla distribuzione degli ingressi/uscite, alla distribuzione del controllo. Nello stesso tempo, gli azionamenti a velocità variabile hanno sostituito molte delle tecniche tradizionali di Motion Control. In aggiunta al controllo preciso dei processi e all’efficienza energetica migliorata, gli azionamenti a velocità variabile hanno aiutato i costruttori di macchine anche a conformarsi più facilmente agli standard di sicurezza vigenti e a ridurre la complessità degli impianti. Negli azionamenti a velocità variabile, l’uso delle tecnologie elettroniche e del software ha permesso di creare nuove soluzioni nella gestione delle tradizionali funzioni di sicurezza come la STO – Safe Torque Off , la SS1- Safe Stop 1, la SSE – Safe Stop Emergency, e così via.
Nuovi scenari: la comparsa dei fieldbus
L’avvento dei bus di campo (fieldbus), ha cambiato gradualmente la situazione e favorito la riduzione del cablaggio, offrendo nuove opportunità in termini di flessibilità di progettazione, modularità, test e manutenzione. Oggi, gli stessi vantaggi si manifestano nei circuiti di sicurezza, che possono essere distribuiti grazie ai fieldbus di sicurezza: i circuiti sono diventati meno complessi, mentre la riduzione di cavi e connessioni ha migliorato l’affidabilità, reso più semplice la manutenzione e facilitato la riconfigurazione del sistema. Uno dei vantaggi più tangibili dati da questa nuova tecnologia è l’accessibilità da parte dellìoperatore al processo produttivo grazie alla riduzione delle barriere fisiche di sicurezza in favore di funzioni di sicurezza di ultima generazione gestite via software.
Perché per gestire la sicurezza occorrono dei fieldbus particolari? Perché i fieldbus convenzionali non sono adatti per la trasmissione dei controlli relativi alla sicurezza, essendo richiesti specifici meccanismi di rilevamento e prevenzione degli errori senza i quali non è possibile identificare i guasti in modo tempestivo. Sono perciò necessarie delle funzioni addizionali, garantire dai protocolli di sicurezza, che possano rilevare errori nella trasmissione dei dati quali ripetizione, perdita, inserimento, sequenza errata, danneggiamento dei messaggi, ritardo, permettendo inoltre di inviare anche i normali dati di processo. Ma vediamo più da vicino le principali caratteristiche di alcuni dei fieldbus nati in funzione della sicurezza.
SafetyBUS p
SafetyBus p è un bus aperto basato sulla tecnologia CAN (Controller Area Network), adatto per l’uso in sistemi di sicurezza fino a EN 954-1 Categoria 4 e applicazioni SIL 3 secondo IEC 61508. Esso consente di connettere fino a 64 dispositivi su una rete avente una lunghezza massima di 3,5 km. I principali vantaggi di SafetyBus p sono i tempi di reazione rapidi, la comunicazione sicura tra funzioni di sicurezza e funzioni di automazione standard, l’integrazione di avanzate funzionalità diagnostiche, il collegamento aperto ai più diffusi bus di campo standard, la grande flessibilità in caso di ampliamento dell’impianto e la semplicità di programmazione e installazione grazie a blocchi software certificati. Su SafetyBUS p la trasmissione dei segnali di sicurezza avviene in maniera separata a livello fisico e logico rispetto ai dati standard. I normali processi di automazione del’impianto perciò non influiscono in alcun caso sulle funzioni di sicurezza. Infine, SafetyBUS p funziona in modalità event-oriented, nella quale i messaggi vengono inviati solo nel caso in cui lo stato degli I/O o il numero di dispositivi connessi variano, garantendo bassi tempi di reazione.
Safety over Ethercat (FSoE)
Per realizzare la comunicazione sicura dei dati sulla rete ad alte prestazioni Ethercat è stato sviluppato il protocollo FSoE, certificato TÜV al livello SIL3/IEC61508. Si tratta di un protocollo che permette la coesistenza di informazioni di sicurezza e standard nello stesso sistema di comunicazione a canale singolo; la soluzione è indipendente dai supporti di comunicazione e dal meccanismo di rilevamento degli errori, oltre a non presentare limitazioni quanto alla lunghezza dei dati di sicurezza, alla velocità di trasmissione e al tempo ciclo. L’FSoE è in grado di gestire errori nei dati quali corruzione, ripetizione, scambio, perdita, ritardo, e indirizzamento non valido. Tra le varie misure di sicurezza vi è l’assegnazione di un numero di sessione e di un identificativo univoco per ogni connessione.
Profisafe
Nella grande famiglia basata su Profibus, anche Profisafe è un protocollo che unisce comunicazioni standard e di sicurezza su un unico fieldbus, permettendo di collegando sulla stessa rete dispositivi standard e dispositivi con funzionalità di sicurezza. Adatto sia per reti Profibus sia per reti Profinet, questo protocollo segue un approccio alla sicurezza chiamato ‘Black Channel’, che non ha impatto sul bus di campo sottostante ed è indipendente dal mezzo fisico di trasmissione. Utilizzabile anche in modalità wireless, Profisafe è stato sviluppato in accordo con lo standard Safety IEC 61508 e previene potenziali errori di indirizzamento, ritardi, ecc. sul bus, con tecniche come la numerazione consecutiva dei pacchetti dati, il monitoraggio del tempo di trasmissione e dell’autenticità dei messaggi, e così via.
AS-interface ‘Safety at Work’
Concludiamo con AS-interface, un fieldbus master-slave conforme alla norma EN 50295. Il mezzo trasmissivo è costituito da un semplice doppino in rame con un’elevata immunità ai disturbi elettromagnetici. Ogni rete AS-i è formata da un master, un alimentatore dedicato e più slave per la connessione dei sensori e degli attuatori. L’alimentazione per i sensori e per l’elettronica degli slave sulla rete è garantita da un’alimentazione disaccoppiata (30 Vcc) dai dati.
Con AS-i ‘Safety at Work’ è possibile eliminare il cablaggio parallelo per il circuito di emergenza utilizzando un unico mezzo trasmissivo per la gestione dei segnali e delle indicazioni rilevanti per la sicurezza. E’ da notare infine che il bus AS-i può essere definito fino alla categoria di rischio più alta (Cat. 4) prevista dalla norma EN 954-1 ed è possibile assegnare i dispositivi di emergenza della rete a slave sicuri.
Il quadro normativo di riferimento
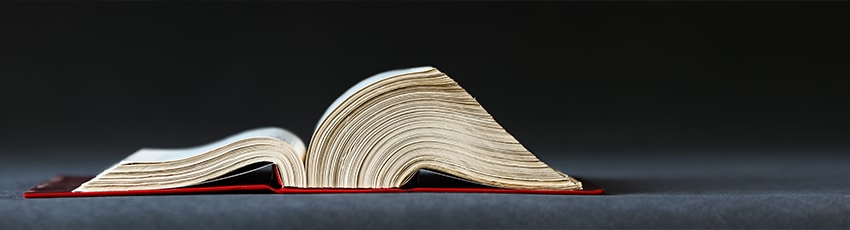
Le norme armonizzate in materia di Sicurezza Macchine si dividono in tre tipi: le Norme di tipo A, di tipo B e di tipo C. Le norme di tipo A (o norme base) definiscono i concetti fondamentali, i principi di progettazione e gli aspetti generali validi per tutte le macchine. Le norme di tipo B (o norme gruppo) trattano un aspetto specifico della sicurezza o un dispositivo di sicurezza. Infine, le norme di tipo C (o norme famiglie di macchina) trattano i requisiti di sicurezza richiesti per ogni tipologia di macchina. Alcune norme in materia di sicurezza sono, per esempio, la EN/ISO 12100 (tipo A) – Sicurezza del macchinario. Concetti fondamentali di valutazione e riduzione del rischio; la EN/IEC 62061 (Tipo B) – Sicurezza di funzionamento di sistemi di controllo elettrici, elettronici, ed elettronici programmabili; la EN/ISO 13849-1 (Tipo B) – Parti dei sistemi di comando legate alla sicurezza; la EN/IEC 60204-1 (Tipo B) – Componenti elettriche delle macchine e la EN 1037 (Tipo B) – Protezione contro l’avviamento imprevisto. Secondo la norma EN/ISO 12100, ove non sia possibile la costruzione conforme a principi di progettazione sicura, è necessaria l’adozione di misure tecniche di sicurezza, come l’installazione di ripari fissi o mobili, rilevatori di presenza per evitare avviamenti imprevisti, ecc. Le misure tecniche di sicurezza devono impedire l’accesso o il contatto involontario con un elemento pericoloso che implica un rischio di lesione personale, oppure ridurre il rischio portandolo ad uno stato sicuro prima che la persona possa entrare in contatto con esso. Affinché una macchina (o altra apparecchiatura) possa essere ritenuta sicura è necessario valutare attentamente i rischi che potrebbero derivare dal suo utilizzo, come indicato dalla norma EN/ISO 12100.

The challenges of Industry 4.0
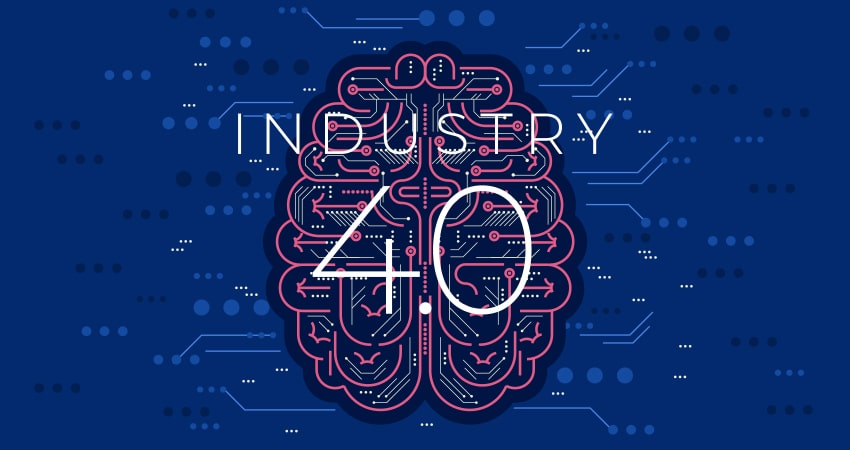
In un ambiente di produzione tradizionale, con linee o celle spesso progettate per la produzione di un solo tipo di prodotto, la gestione della sicurezza è generalmente semplice: una valutazione del rischio di tutti gli aspetti dell’operazione – dai singoli componenti fino ai “punti di contatto” dell’operatore con le apparecchiature – permette infatti di creare una guida che rimarrà valida fino a quando l’uso della linea cambierà o si apporteranno delle modifiche ai suoi componenti. I rischi possono quindi essere ridotti al minimo, purché siano seguite le procedure corrette. Al contrario, un impianto che opera secondo i nuovi principi di Industry 4.0 presenta potenzialmente una serie di problemi molto diversi e più complessi. Tra questi, per esempio, i problemi di sicurezza creati dalla riconfigurazione delle aree di produzione con breve preavviso, che implica i rapidi cambiamenti di attrezzature e persino il movimento fisico dei componenti. Esiste tuttavia una varietà di tecnologie disponibili per contrastare questi problemi – e non è esagerato affermare che Industry 4.0 offre persino l’opportunità di aumentare ulteriormente la sicurezza grazie alla capacità di raccogliere dati in tempo reale e intervenire prima che un potenziale pericolo diventi reale. Oltre a garantire una maggiore sicurezza, ciò consente anche di introdurre nuove applicazioni importanti, come la manutenzione predittiva. Infine, la possibilità di ottenere una rappresentazione logica dell’impianto (Digital Twin) permette di simulare tutte le situazioni di pericolo che potrebbero verificarsi, intervenendo quindi a priori con le necessarie misure correttive.
La sicurezza nei sistemi di Motion Control
Benché in passato la sicurezza non abbia fatto parte intrinsecamente dei sistemi di Motion Control, la situazione è cambiata nel tempo. Come abbiamo visto, la sicurezza era inizialmente affidata a dispositivi elettromeccanici, non essendo previste dalle norme soluzioni di altro tipo. D’altra parte, l’affidabilità reale o percepita delle soluzioni elettroniche o software non aveva ancora raggiunto i livelli attuali. L’avvento dei fieldbus e dell’automazione distribuita ha modificato lo scenario, permettendo di localizzare i dispositivi di sicurezza nei punti più opportuni (pulpiti di comando, sala controllo, ecc.) e, nello stesso tempo, di introdurre le prime soluzioni software. Dispositivi come i variatori di velocità, gli inverter e i Motion Controller centralizzati hanno permesso di concentrare la gestione della sicurezza a monte del sistema, semplificando il controllo delle singole unità di Motion e rendendole più accessibili. E’ stato infatti possibile sostituire le unità blindate con unità dotate di semplice carter, essendo la protezione garantita da caratteristiche e funzioni non più locali ma distribuite sull’impianto. Oggi si comincia a parlare di Safety 4.0, con ciò facendo riferimento a sistemi di sicurezza più flessibili e versatili, rispondenti alla potenziale necessità di continue modifiche dell’impianto per soddisfare nuove esigenze del mercato.
In questo campo AMK propone sistemi da quadro (centralizzati) come ad esempio le serie KE e KW, oltre ad azionamenti nearby (architettura decentralizzata) come la serie iX, e ancora souzioni integrate motore più azionamento come la serie iDT5. Essendo la safety trasmessa via rete, e quindi via cavo, i noti vantaggi di un sistema distribuito si traducono, anche in questo caso, una semplificazione dei cabalggi, in quanto non viaggerà più su un supporto dedicato ma su rete EtherCAT condivisa.