For the designer who is about to build a machine, it is important to understand the pros and cons offered by each solution-whether, centralized with a […]
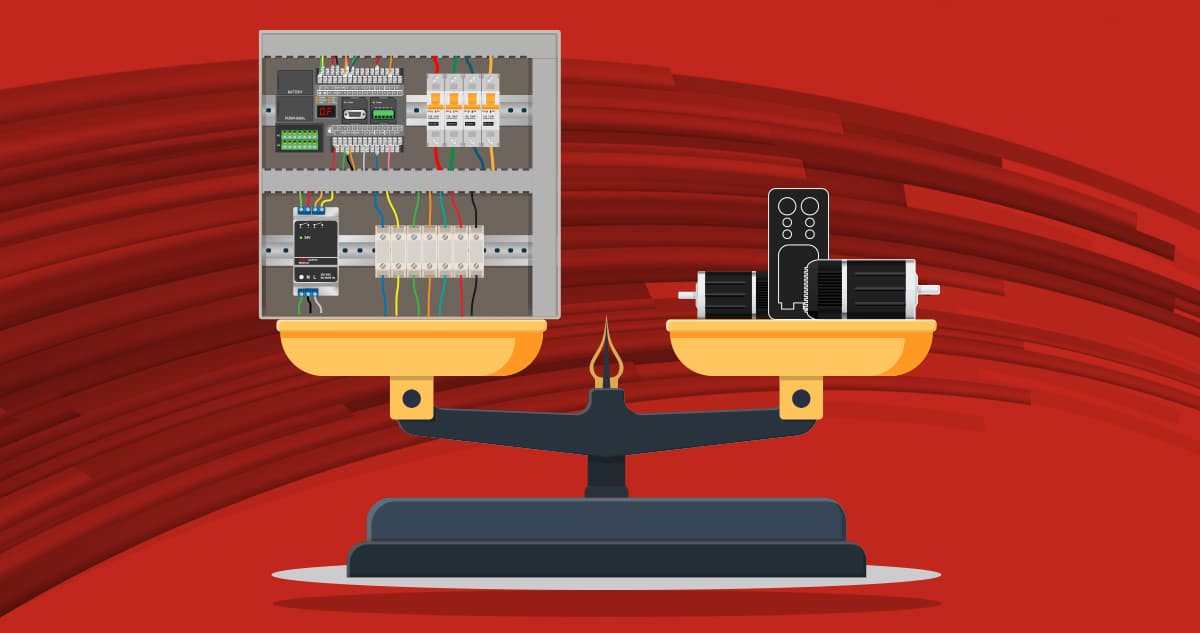
For the designer who is about to build a machine, it is important to understand the pros and cons offered by each solution-whether, centralized with a panel drive or decentralized with distributed drives-since, some choices need to be made early in the design phase.
In decentralized architectures, power and control electronics are usually integrated directly into the motor housing or placed close to it. The footprint of the electronics thus shifts from the control cabinet to the machine edge. The now well-known advantage of this is thus to free up space in the cabinet, resulting in reduced footprint and wiring.
However, while this may be an irrefutable advantage, depending on the situation and one’s objectives, critical issues may arise, so it becomes important to put the choices into context and be aware of the possible “side effects” of one or the other solution.
Below, we will deal one by one with the aspects that we consider worthy of preliminary analysis, hoping to do the planner reader a favorable thing.
The footprint of motors with integrated electronics
The fact that the power and control electronics are remotely located on (or near) the motor does not mean they disappear. It does mean that our application will have to have enough space near the motor to take into account the additional thermal issues introduced by the presence of the drive.
For example, synchronous servo motors, often used in industrial applications, are optimized for dynamic operation and are often integrated into the machine structure to optimize space. Adding a component into an already “crowded” situation, effectively increasing the size of the motor, is not always possible.
Technological evolution is meeting designers as drive manufacturers challenge themselves to develop highly efficient power amplifiers without compromising compactness. Conversely, it must be said that next-generation composite material semiconductors such as SiC (silicon carbide) modules, which allow them to work at high voltages and temperatures while demonstrating a high efficiency, remain much more expensive than the more classical IGBT (insulated-gate bipolar transistor) modules. Indeed, to date, there is a lack of processes to produce SiC modules at low cost, and the industry is looking to the future in hopes of change in the years ahead.
Thermal model, interfaces, and sensors
Another aspect to be taken into account in the design phase is heat development. This makes “smart” thermal management of drives extremely important, which cannot be limited to classic protection by calculating I2t. In fact, software plays a key role today, which, based on thermal models, can provide information related to the heat balance, marking the designer’s way to optimal heat management according to the environment and the system, taking into account multiple variables such as temperature, humidity, solar radiation, indoor or outdoor environment, etc.
Decentralized drives should also be equipped with multifunctional bus interfaces to be more versatile. There is expected to be an increasing use of devices that can be expanded and scaled as needed by adding option cards and interfaces.
Last but not least, the integration of sensors driven by the IIOT (Industrial Internet of Things) of Industry 4.0 will shape trends in the design and implementation of sensors in predictive maintenance activities, along with cloud connectivity and artificial intelligence for remote data analysis and monitoring. Sensors will be the link between the physical systems, which collect machine process data, and the communication links that transmit the data to the cloud or other control or monitoring facilities.
Wiring
Cables are the backbone of industrial automation systems. The past two decades have made us witness a technological development that has changed the nature of industrial production today.
This evolution has generated a demand for super-performance solutions. There is a growing trend among system manufacturers toward hybrid solutions, where power, fieldbus, 24 V voltage, and STO coexist in a single compact and lightweight line with a daisy chain structure.
High levels of flexibility, stability, and durability from all parties involved integrated and system cables, therefore, become necessary to support these changes since the failure of only one of these links would lead to downtime and substantial cost-effective losses.
Possible voltage drops should certainly be considered during design, keeping in mind the current-carrying capacity of the limited cable cross section.
Depending on the application, the motor’s overload behavior should be considered. “Smart” wiring technology in daisy chain design and hybrid cables minimizes wiring effort and simplifies possible machine expansion.
Choosing the motors
Choosing the motor type depends not only on the required performance in terms of torque, speed, etc., but also on the integration with the mechanics on the machine board and the environment in which it will operate. Choosing whether to drive the motors with a drive housed in the electrical cabinet, from a drive collated near the motor or even integrated into it, will depend on the correct evaluation of all the aspects discussed so far. That is why, as early as now, the success of an application will depend more and more on the correct evaluation of electrical, thermal, mechanical, and information aspects.
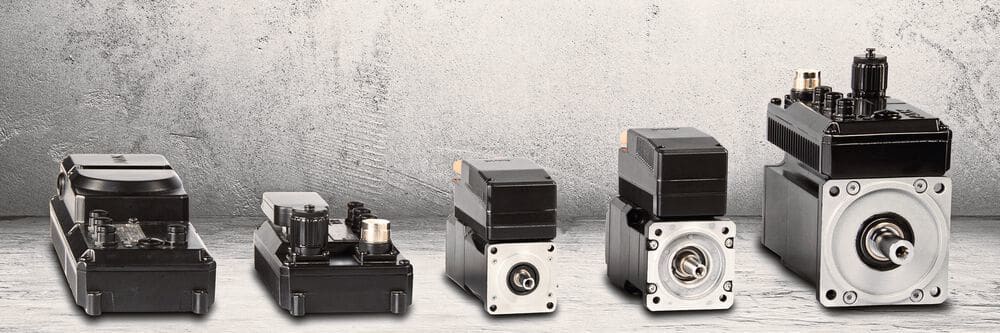
There is no black or white. The advantages are in the middle
To conclude, by taking up the title of this article, the answer is that it depends. There is no such thing as a better architecture; to properly choose one or the other solution, it is important to understand its pros and cons.
What we can tell you is that it is rarely black and white. Mixed solutions are often the best choice, where centralized and decentralized drives are combined. This flexibility keeps all doors open and allows a greater range of needs to be covered.
In short, both architectures have their raison d’être, and in real applications there will always be a need for both centralized and decentralized drives. Rarely does one choice exclude the other, and in most cases, one will have to opt for hybrid solutions. Both configurations can work together, complementing each other.