Un modo perfetto per migliorare produttività, precisione e prestazioni dinamiche Forza e accuratezza per le macchine utensili grazie sistemi di azionamento completi con motori lineari o […]
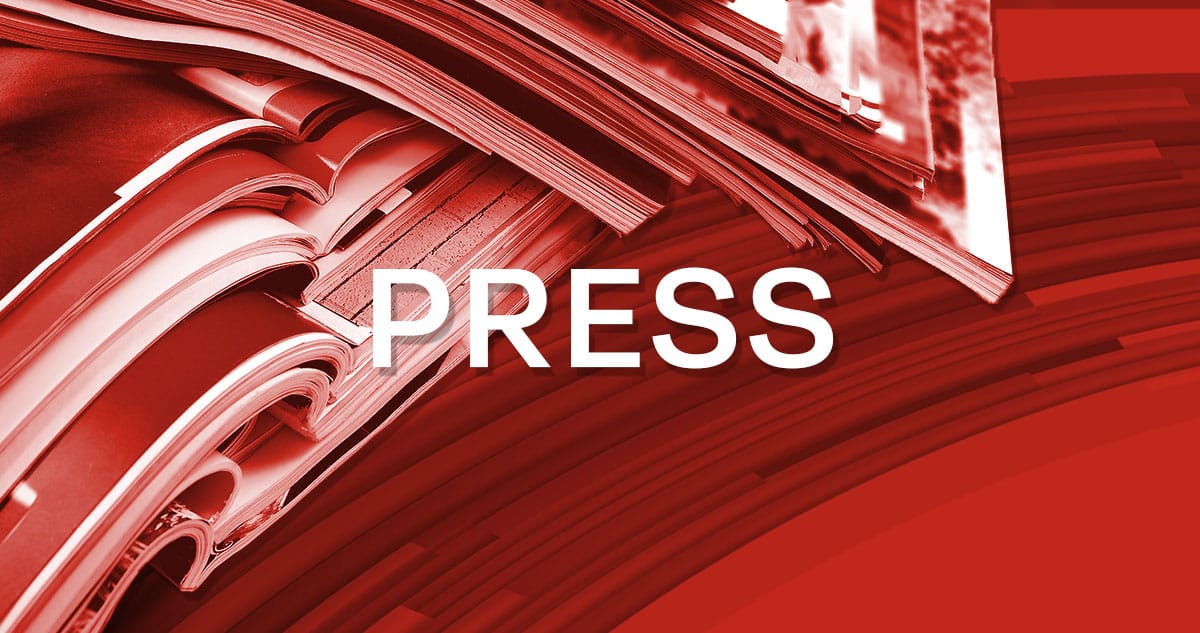
Un modo perfetto per migliorare produttività, precisione e prestazioni dinamiche
Forza e accuratezza per le macchine utensili grazie sistemi di azionamento completi con motori lineari o torque ed encoder assoluti.
di Sofia Rossi
Con oltre 40 anni di esperienza nell’automazione industriale, Servotecnica è uno dei principali fornitori al mondo di soluzioni meccatroniche e componenti elettromeccanici su misura per svariati settori industriali. In particolare, per i costruttori di macchine utensili l’offerta tecnologica di Servotecnica si avvale della combinazione tra i motori direct drive dell’olandese Tecnotion e gli encoder assoluti dell’austriaca Flux. Il punto di forza dell’azienda è la combinazione di tecnologie innovative con l’esperienza e la competenza dei propri tecnici. Ne parliamo con Massimo Redaelli, technical director Servotecnica.
Motori direct drive: cosa sono e come funzionano
I motori direct-drive di Tecnotion, proposti in Italia da Servotecnica, come indica la parola stessa, sono motori che permettono l’accoppiamento diretto al carico, senza bisogno di alcun elemento intermedio tra l’organo che deve trasmettere il moto, il motore, e ciò che deve essere movimentato, ovvero il carico. “Nella meccanica tradizionale, solitamente per generare un movimento lineare, viene utilizzato un motore rotativo che, per mezzo di una catena cinematica, costituita da una cinghia, un pignone a cremagliera oppure una vite senza fine, trasforma il movimento da rotativo a lineare. In genere, viene inserito anche un riduttore per ottimizzare i rapporti di inerzia tra il carico e il motore e per far lavorare il motore il più possibile vicino al suo punto di funzionamento nominale. Nei motori direct-drive, invece, per generare un moto lineare si utilizzano delle bobine che, opportunamente alimentate dai classici inverter, azionamenti elettrici o convertitori di potenza, e quindi attraversate da una corrente alternata trifase, generano un campo elettromagnetico “traslante” (oppure “rotante” nel caso dei motori rotativi), cioè una sorta di onda elettromagnetica su cui il motore “surfa” generando il moto rettilineo”, spiega Massimo Redaelli, technical director Servotecnica. “Perciò, i motori lineari possono essere pensati come motori con un funzionamento analogo a quelli rotativi, ma srotolati e disposti su un piano”, precisa.
In effetti, il rotore con i magneti permanenti diventa la parte fissa del motore lineare, mentre lo statore (con gli avvolgimenti delle bobine) costituisce la parte mobile. Nel dettaglio, questa configurazione può essere visualizzata come una sorta di “cremagliera” elettromagnetica, dove il pignone rappresenta il campo magnetico rotante, mentre l’ingranaggio dentato rappresenta i magneti permanenti statici: le forze di attrazione e repulsione che si producono tra le bobine e la traccia di magneti permanenti permettono di convertire l’energia elettrica in energia meccanica lineare con un elevato grado di efficienza, creando il moto necessario. La velocità del cambiamento di corrente determina la velocità del moto, mentre l’amperaggio della corrente determina la forza generata. Questo principio di azionamento diretto, quindi, si basa sull’utilizzo di una forza magnetica che muove un gruppo di bobine lungo una traccia di magneti permanenti.
I vantaggi dei motori diretti
Uno dei vantaggi principali dei motori diretti, sia lineari che rotativi (motori torque) è l’eliminazione dei cosiddetti componenti “elastici” della trasmissione, come i riduttori e gli accoppiamenti, che possono creare problemi di gioco e di risonanza. “Di conseguenza, la larghezza di banda, che in gergo tecnico viene definita “banda passante”, e la rigidità del sistema di movimentazione possono essere molto più elevate rispetto ad un motore tradizionale, a garanzia di una maggiore precisione, una dinamica superiore e una migliore ripetibilità e accuratezza nel posizionamento”, afferma Redaelli. In assenza di parti meccaniche aggiuntive soggette ad usura meccanica, il controllo del movimento può essere reso molto più stabile nel tempo. Quindi, senza usura meccanica, gli utenti delle macchine godono di un’affidabilità e di una durata esemplari. Anche il TCO (costo totale di proprietà) si riduce rispetto alle soluzioni tradizionali. In aggiunta, la mancanza di elementi meccanici che comportano inevitabilmente degli attriti responsabili di perdite, si traduce anche in una maggiore efficienza energetica.
“Un altro vantaggio significativo è che non avendo più cinematismi di conversione intermedi, come viti a ricircolo di sfere, cinghie e pulegge, riduttori o sistemi a cremagliera, che sono necessari nei motori tradizionali per convertire il moto rotatorio in moto lineare, i motori direct-drive offrono un’efficienza e un’accuratezza posizionale molto superiori, anche a velocità elevate, consentendo al contempo un movimento estremamente fluido in tutto il campo operativo del motore.
Un altro importante aspetto da considerare è lo spazio. Il fatto che la parte mobile di un motore lineare sia accoppiata direttamente al carico riduce l’ingombro e semplifica la configurazione della macchina, il che rappresenta un notevole vantaggio sia per i progettisti che per gli utilizzatori del sistema. Tutti questi vantaggi rendono i motori lineari Tecnotion molto interessanti per il settore delle macchine utensili”, precisa Redaelli.
Le peculiarità dei motori iron-core e iron-less
Uno degli svantaggi dei motori iron-core a magneti permanenti, maggiormente utilizzati in ambito industriale perché permettono di esprimere la maggiore potenza (forza di spinta) per unità di volume, è il cogging, una forza parassita prodotta dalla generazione (da parte dei magneti permanenti) di una forza di attrazione fluttuante che attira i materiali magnetici, come il ferro. “Questa forza, che deriva proprio dalla forma costruttiva di questi motori, a causa della presenza dei “denti” di materiale ferromagnetico nella struttura contenente gli avvolgimenti (primario), compromette la fluidità di movimento di ogni motore iron-core”, spiega Redaelli. “Ciascun dente, infatti, muovendosi affacciato alla piastra magnetica (secondario), ha delle posizioni preferenziali che si trovano in corrispondenza di ogni magnete. In queste posizioni il dente – che, ricordiamolo, è di ferro – è attratto dal magnete e si trova in condizione di equilibrio stabile, in corrispondenza dell’asse polare. Durante il movimento lungo la piastra magnetica si passerà da una posizione di equilibrio stabile alla successiva, attraversando la posizione instabile, corrispondente all’asse interpolare. Questo causa dei “sobbalzi” indesiderati durante il movimento”, continua Redaelli.
Per limitare il ripple di velocità introdotto dal cogging è fondamentale utilizzare un motore che sia stato progettato per avere un cogging ridotto. Tra i possibili accorgimenti per la riduzione del cogging, la peculiarità distintiva dei motori direct-drive di Tecnotion, proposti in Italia da Servotecnica, risiede nell’unicità del progetto elettromagnetico del motore.
“La soluzione di Tecnotion – precisa Redaelli – è quella di inclinare leggermente i magneti rispetto alla direzione di moto, in modo da aumentare, in modo più graduale rispetto alla conformazione a denti dritti, l’area di affaccio tra dente e magnete, quando ciascun dente passa sopra a ciascun magnete. È quello che succede ad esempio quando si prende un dosso con una macchina: se lo si prende ortogonalmente l’impatto col dosso è notevole, se si inclina leggermente la direzione di ingresso l’impatto è minore. L’effetto dell’inclinazione dei magneti agisce in favore di una riduzione del cogging”.
Un secondo accorgimento consiste in un attento dimensionamento dei gioghi, in particolare quelli di richiusura all’inizio e alla fine, che sono regolabili e influenzano il cogging, in funzione di una minimizzazione del fenomeno.
La speciale tecnologia degli avvolgimenti bobina consente di ottenere una bobina che, a parità di corrente, sviluppa un flusso molto maggiore rispetto alle altre bobine sul mercato, estremamente ripetibile e ben collimato, ovvero con linee di flusso perfettamente parallele.
“Il fatto di avere una bobina ‘forte’ nel primario del motore ha permesso a Tecnotion di utilizzare magneti più piccoli nella parte secondaria – spiega Redaelli. Questa scelta porta con sé il vantaggio di avere passi magnetici ridotti rispetto a quelli della concorrenza, che rendono i motori Tecnotion molto interessanti per il settore delle macchine utensili”.
Avere magneti più piccoli permette infatti di ridurre non solo la forza di attrazione, anche della metà, il che diminuisce l’attrito sulle guide e il cogging, ma anche la sezione del ferro della guida magnetica del motore (Back Iron), che essendo più sottile risulta anche più leggera, in media del 30%. Questo comporta un notevole risparmio nei costi, oltre a una riduzione della taglia dei motori che è possibile impiegare in macchine a portale per taglio laser.
La gamma dei motori direct-drive Tecnotion include anche versioni ironless, per applicazioni con dinamiche molto spinte. Questo tipo di motori sono generalmente da preferirsi nelle applicazioni con un carico utile leggero che necessitano di movimentazioni estremamente accurate o di un’accelerazione molto elevata.
Nei motori ironless, in cui non c’è forza di attrazione né cogging tra il gruppo delle bobine e la traccia dei magneti per l’assenza di ferro, intervengono altri aspetti costruttivi legati agli aspetti termici: la più alta resistenza termica rispetto ai “fratelli” ironcore comporta un più difficile smaltimento del calore e una spinta continuativa più bassa.
Accuratezza nel controllo degli assi e del funzionamento del motore
Affinchè un motore diretto, lineare o torque, possa offrire un funzionamento altamente prestazionale, affidabile e durevole, è necessario utilizzare encoder, lineari o rotativi, e azionamenti che garantiscano le stesse caratteristiche.
Per quanto riguarda gli encoder, la proposta di Servotecnica guarda all’azienda austriaca Flux che, forte di oltre 40 anni di esperienza nel campo dei sistemi encoder, nel 2017, ha introdotto sul mercato un prodotto innovativo nel campo dei trasduttori basato sulla tecnologia Giant Magneto Impedance (GMI). Si tratta di trasduttori GMI, che si collocano a metà strada tra quelli magnetici e quelli induttivi, unendo i pregi dell’una e dell’altra tipologia; superano, infatti, i limiti delle tecnologie puramente magnetiche, essendo esenti dagli effetti di isteresi, e consentono di ottenere accuratezze molto simili a quelle degli encoder ottici. Rispetto a quest’ultimi, tuttavia, sono più robusti e semplici da installare, essendo per loro natura immuni dalle contaminazioni presenti negli ambienti produttivi delle macchine utensili e non richiedendo di essere protetti e incapsulati, con una serie di accorgimenti in termini di pulizia, pressurizzazione e filtrazione dell’aria che ne complicano l’utilizzo, come avviene per quelli ottici.
Per le macchine utensili, la gamma di trasduttori Flux è studiata per garantire massima fluidità di moto nel controllo del movimento degli assi sulle macchine.
Anche l’azionamento ha un ruolo fondamentale. Nell’ambiente industriale, per garantire prestazioni elevate e un’alta efficienza energetica è necessario utilizzare azionamenti ad alte prestazioni, caratterizzati da determinati requisiti in termini di frequenza di campionamento degli anelli di corrente e di velocità di elaborazione dei dati. Tutt’e tre gli elementi – motore diretto, azionamenti ed encoder – contribuiscono ad una qualità di moto superiore rispetto ad altri sistemi di movimentazione e cinematismi.
Progetti su misura, supporto tecnico e assistenza post-vendita
Con oltre 40 anni di esperienza nel mercato dell’automazione industriale, il team di Servotecnica è in grado di offrire un supporto altamente qualificato in termini di consulenza nella scelta del prodotto e della tecnologia migliore per la specifica applicazione, in funzione delle esigenze delle macchine e del cliente, e nella gestione dei progetti di integrazione del motore all’interno della macchina, lavorando in partnership con i costruttori e fornendo indicazioni in merito alle lavorazioni meccaniche, al dimensionamento e fissaggio del motore, alle tipologie di montaggio e alle tolleranze meccaniche, al fine di garantire le massime prestazioni in termini di potenza, precisione, ripetibilità e accuratezza di posizionamento.
“Il know-how dei nostri ingegneri applicativi è a disposizione durante l’intero processo di selezione, progettazione e sviluppo dei prodotti giusti per l’applicazione del cliente. L’azienda offre anche un servizio di co-progettazione. È capitato che il cliente ci abbia commissionato delle parti di macchina, che prevedevano la fornitura del motore torque già integrato in una parte meccanica, provvista di freno, riduttore, encoder, tutto in un unico blocco da montare come un classico motore composto da flangia e albero. Alla vendita di un motore, inoltre, è spesso associata anche quella relativa alla parte di controllo: in questo caso, il nostro contributo riguarda la messa in servizio, l’assistenza tecnica post-vendita e il customer care, piuttosto che il supporto alla programmazione della macchina”, afferma Redaelli.
Al supporto e alla fornitura di componenti elettromeccanici di altissima qualità, si affiancano, inoltre, un servizio di riparazioni e test di qualità, comprensivo di certificazioni per mercati specifici per adeguarsi agli standard industriali, rilasciate a seguito di rigorosi test di qualità, e servizi logistici avanzati end-to-end, con oltre 3.000 prodotti a magazzino, per supportare le esigenze speciali dei clienti, consegnando ogni singolo componente nel modo migliore, con rapidità e imballaggi specializzati.