Introduction The integration of Slip Rings into SCARA robots is a significant advancement in industrial robotics. SCARA (Selective Compliance Assembly Robot Arm) robots are valued for […]
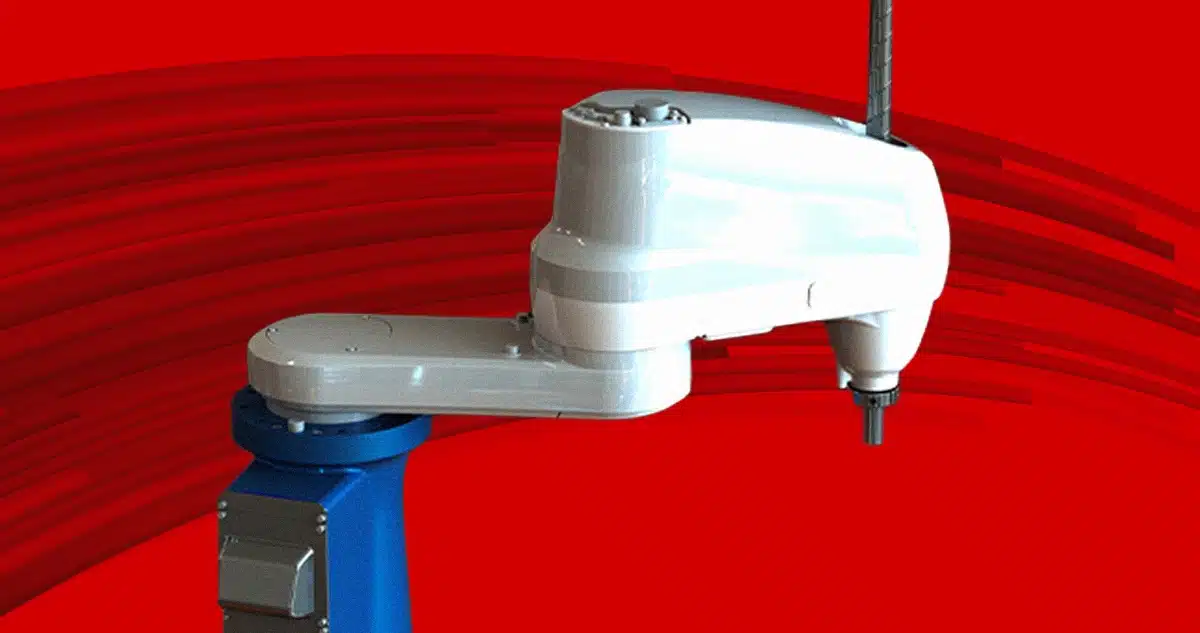
Introduction
The integration of Slip Rings into SCARA robots is a significant advancement in industrial robotics. SCARA (Selective Compliance Assembly Robot Arm) robots are valued for their speed and precision of movement, finding application in areas such as assembly, pick-and-place, and other industrial areas where efficiency and accuracy are essential.
Slip rings, or electric rotary joints, play a crucial role by enabling the continuous transmission of electrical power and data signals between the fixed and rotating parts of a system, eliminating common problems such as cable wear, entanglement and twisting. This is particularly advantageous in SCARA robots, where the need for complex rotary movements is a distinguishing feature.
Typically, the Slip Ring is mounted on the last axis of the SCARA robot, a detail we will examine later to understand its importance, the challenges it poses and the consequences on system performance. This integration facilitates continuous or semi-continuous rotation of the robotic arm, improving overall efficiency.
With the advent of recent innovations, modern Slip Rings can now support the transmission of high-frequency signals, Ethernet data, and fibre optics, further enhancing the performance of SCARA robots. This technological advancement opens new frontiers in industrial automation, enabling faster communication that results in more precise motion control and higher throughput.
In this article, we will discuss the advantages of integrating Slip Rings into SCARA robots, delve into recent technological innovations in the field, and ask: how can Slip Ring integration contribute to the evolution of SCARA robot performance? What new opportunities could open up for robot manufacturers and what challenges will they face?
Challenges
SCARA robots are known for their speed and precision in industrial operations. However, some significant challenges arise in their design and use.
Motion Control:
The need to increase operational speed while maintaining a high level of accuracy is one of the main challenges. High-speed signal transmission is crucial to reduce the cycle time and closing time of control loops, which in turn can affect the accuracy and responsiveness of motion control.
Head Structure:
Weight management in the head structure of the robot is crucial, as this part operates over a larger radius and generates significant inertial loads. The design of lightweight and reliable components is crucial to ensure that the robot can operate effectively without overloading the mechanics or compromising precision in operations.
These challenges highlight the inherent complexity in the design and implementation of high-performance SCARA robots. Identifying and overcoming these challenges is essential to further improve performance and push the limits of what is possible with SCARA robotics technology.
Solutions
To overcome the challenges associated with the design and operation of SCARA robots, several innovative solutions were devised. Some of these solutions are described below, focusing on improved motion control and optimised head structure management.
Improved Motion Control:
High-frequency fieldbus transmission through Slip Rings can reduce the cycle time and closing time of control loops, enabling more precise and responsive motion control. Slip rings alone can provide high performance; however, for extreme transmission performance, FORJs (fibre optic rotary joints) can be optionally integrated to provide high-speed data transmission without electromagnetic interference. Servotecnica can provide combined solutions that integrate both Slip Rings and FORJs, and develop the MUX/DEMUX electronics, contributing to the optimisation of motion control in SCARA robots, fostering faster communication and more precise operations.
Optimisation of the Head Structure:
The design of lightweight and reliable Slip Rings is crucial to effectively manage weight in the head structure. A lightweight Slip Ring reduces inertial loads, increases throughput and helps maintain the robot’s operational efficiency. Furthermore, a design that allows the Slip Ring to support radial and axial forces can be integrated into the customer’s mechanics, further contributing to a reduction in weight and the number of components required, without compromising the reliability or performance of the system. Designing tailor-made solutions that exactly meet the needs of the application, avoiding redundant components, is an effective approach to achieve the minimum necessary for the application, allowing further optimisation in terms of weight and functionality.
These solutions represent significant steps towards overcoming the challenges associated with motion control and head structure management in SCARA robots. By implementing these technologies, it is possible to push the performance of SCARA robots to new levels, bringing tangible benefits in terms of efficiency and precision in a wide range of industrial applications.